|
|
Quick Bid - 05.10.04 The Item Detail Labor Cost Tab: Setting Base Production - QB
Views: 475 Last Updated: 10/31/2024 12:46 pm |
0 Rating/ Voters
|
    |
Be sure to rate this article 5 Stars if you find it helpful! |
Once you have decided who is going to perform the Labor (Payroll Class/Crew/Installers), you need to set up the Base production values - how much of Material/Labor can the Crew install/perform in a day. ProductionDepending on how you define Labor, enter a production default value either by the hour or by the day, or enter the labor cost in the Price column. These three values are linked together, changing one value updates the other two columns. The "Price" is based on the Wage settings for the Payroll Class (or Classes) listed in the upper grid, less Burdens, Markups, and Indirect Expenses, of course. 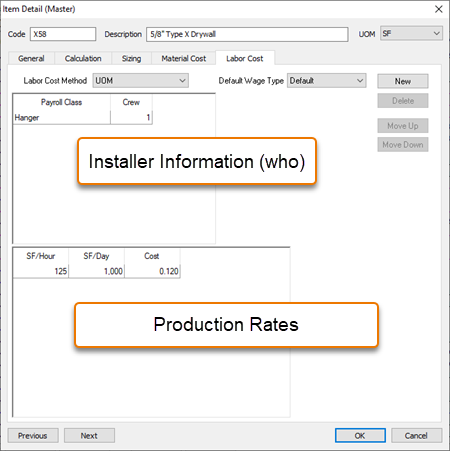
- Changing Crew size does not affect production (how much x gets done/built/installed in y amount of time), but it does change labor price. The production values (x/hour, x/day) are stored values meaning these production rates stay the same no matter how many crew members are specified (you will still get x/day done, it just takes more or less Crew to do it...). The production rates or Price must be manually changed for the new Crew Size.
- Changing a pay rate in the Payroll Tables does not change production. It does change the unit labor costs resulting from the production settings. For example, if you increase the Wage for the Payroll Class listed in the upper section, your Production (sf/hour or sf/day) doesn't change but your price does change because it costs you more to get the same amount of work done.
The Item Labor Pricing cost is based on the first Wage Type in your Wage Types list when "Default" is selected for Wage Type. The next article shows you an example of how a Item with Labor shows up in the Condition Detail.
|
|